Posted on
May 17, 2010 by
bp complaints
New Deepwater Horizon images:
ROV attempting to activate Deepwater Horizon Blowout Preventer

Image by uscgd8
100421-G-XXXXL-_003_-_Deepwater_Horizon_fire

Image by uscgd8
Deepwater Horizon Oil Spill – MODIS/Terra Detail (with interpretation), May 1, 2010
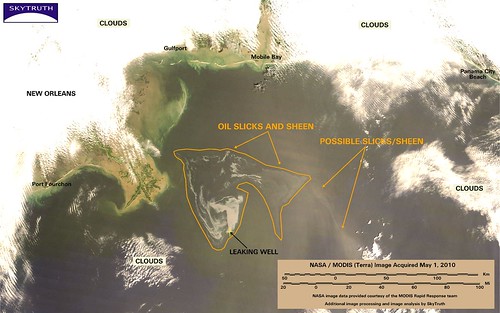
Image by SkyTruth
Tags: Activate, attempting, blowout, Deepwater, Horizon, preventer
Category
News
Trackback: trackback from your own site.
As for the latest plan to insert a 6" pipe into the riser . . . are they planning to put this on vacuum? I cannot imagine it doing much good if simply relying upon the physical properties of the oil for lift. Based on some rough calculations, they are going to need significant lift to move the necessary volume . . . especially if the flow rates are as high as some now claim.
My "HOT TAP" design … including my saddle T design – with two "TAP" ports (one to install a new temp riser and the other to install a gate valve to largely block flow out of pipe once riser attached) and with a flange on the end that would allow pipe to be cut off once the temp riser is attached and capped
This would be installed in the section of riser that is closer to BOP stack and is lying on sea floor … there has to be large sections realtively undamaged … and yess the Choke and kill lines on outside of riser would have to be cut out of way which should be simple, in order for HOT TAP saddle to be installed
This saddle and "T"s again would take less than a day to fabricate … the valves and drill tap etc already exist and bolt on … a cap for the end once cut off would take a few hours more …
There are also no complicated manuvers required to install or operate the ROV’s should be able to easily handle …
Once installed thios provides capture and control – eliminates the leak by capping riser … there is no real risk of over-pressure of old riser as there is never a cap or closed valve without relief in place
By using the large riser pipe they can use the normal rig to attach to riser stack – and they can run smaller pipe inside to collect oil and run warm seawater and CO2 or whatever inside riser outside of the smaller pipe to help carry oil to surface
This is simle and would be completely effective at stopping the leak, and collecting the spilling oil … if nothing else the install this and do nothing more and simply wait for the relief well to be completed
This could have been down 2 weeks ago … and been completed in a couple days
OIL SPILL
After you attach the temp riser pipe to the HOT TAP … put that big containment box on the bottom next to the completed hot tap …. run an arm out from top of it and attach to new riser to stabilize and secure the old riser pipe laying on the bottom … won’t eliminate all movement but would be a big old damper …. heck fill with concrete if necessary once on teh bottom
No sense all that work it going to waste
dsw93,
If you look at Halliburtons well schematic, there are only 2 casing strings cemented back to the wellhead, those are the 28" and 22" conductors,
the rest are drilling liners that are not fully cemented back into their liner laps. Except for the 16" which is a full string back to the wellhead, but it is also not fully cemented. The tapered production string 7" x 9-7/8" is a full string back to the wellhead but it is not cemented back to its lap with the 9-7/8" drilling liner, or to the crossover joint.
This leaves an awful lot of casing exposed to the formation, that you really don’t know how its going to act after having a hole punched in it. For instance you could have high pressure brine in one of those areas that is trying to collapse a relatively weak large diameter casing, Or a layer of poly-halite salt that is plastic and trying to extrude into non-cemented space, this stuff is unrelenting it will squeeze on an unprotected pipe until it collapses. Another hazard is high pressure oil or gas migrating up from one unprotected liner gap to the next until it gets to a liner that will not withstand the pressure and either collapses it or bursts the next one up the hole.
This method of well construction is unprecedented on a wildcat well, it’s doing things on the ultra-cheap, in an unexplored area where you only have a slight clue as to what you might be drilling into.
It was intended for use on production fields where the formations are of a known characteristic and pressures.
Here is the well schematic.
http://www.roughneckcity.com/uploads/ProbertTestimony_5-11-2010.pdf
220mph,
Good idea, I only see on problem and that is with your valve.
There is drill pipe laying in the riser, and you would have to figure out a way to cut it, without cutting the bottom out of the riser.
Since its on the upstream side of the hump in the riser there would be no need for the valve anyway, because once flow stops over the hump it wont go anywhere, unless the hump sinks. They could attach diesel or vegetable oil float bags to it to keep it from sinking back to the seabed.
Another thing to look at is how to get it to seal around all of the jewelry on the riser, the choke and kill lines booster line and hydraulic lines.
What is the logic of inserting a 6" pipe into the 21" riser rather than slipping a 22-24" pipe over the riser? A slight, and I mean slight drop in pressure may occur as the flow enters the larger pipe or the veturi/vortex effect would draw seawater in thru the slip joint without allowing oil to back flow out the joint. Seems like this would elliminate the need for a plug/stopper around the 6" pipe.
Is it technically feasable and practicle to place a hydraulicly powered pump on the bottom to to draw oil out of the riser and pump it to the surface? Something such as done, I believe, with a production well.
Horizon said
"Good idea, I only see on problem and that is with your valve.
There is drill pipe laying in the riser, and you would have to figure out a way to cut it, without cutting the bottom out of the riser.
Since its on the upstream side of the hump in the riser there would be no need for the valve anyway, because once flow stops over the hump it wont go anywhere, unless the hump sinks. They could attach diesel or vegetable oil float bags to it to keep it from sinking back to the seabed.
Another thing to look at is how to get it to seal around all of the jewelry on the riser, the choke and kill lines booster line and hydraulic lines."
Horizon …
If you look at the red ‘schematic’ drawing of the saddle fixture the side opposite the drill "T" port has a matching "T" so you could drill all the way thru the riser – and thru any junk in the riser. And the ram of the valve could likewise go thru the riser pipe.
In reality though I actually don’t think you need this interim process … once the riser is drilled and new riser attached you have pressure relief.
I think you could simply then cut off the end of teh old riser. You would get flow out of the pipe end but as we coudl see by the video yesterday, with the current amount of gas that flow immediately rises and clears the pipe end.
I would cut the old riser maybe a foot or so from the end of my saddle fixture’s bolt flange. I would make the cap slightly longer and out of pipe with a slightly larger ID as the OD of the old riser. That way the old riser becomes the "guide/locater" for the cap … all an ROV needs do is get the end of cap over the old riser pipe and its a simple nmatter to slide it on …
I would have bolts attached to cap so its simple matter to slide on and ad nuts (or even install a pivoted bolt with nut attached and use slotted bolt holes in saddle end flange.
Even if oil was flowing as the cap was pushed on the flow would go out the new riser relief as flow is limited by the cap.
Better yet put a gate valve on end of the cap and leave that valve open until cap isnatlled – then oil and gas simply pass thru and there is no pressure against cap. Once cap is on and bolted close the valve. This gives you ability to attach other stuff to the line as well.
I’m not sure what "hump" you are talking about … I would install the saddle T where old riser is already lying on seabed. You might have to scoop a little out below it to get saddle around it but that would be it.
And I think using the "outhouse" – the containment box that didn’t work – as a stabilizer … attaching the new riser to an arm from the top of containment box and the old riser to a similar arm from bottom of containment box … would support the end of the old riser and the saddle once you cut the old riser away
As far as "sealing" around the old choke and kill lines etc – that is easy – just cut them off the old riser at that point before you place the saddle.
WOrst case if you have to design a couple plates to fit around the riser and the junk with a rubber seal to match sandwiched between them … you don’t need a perfect seal … especially if they think they can get suction on the line from topside as they claim they would do with their silly "straw and stopper" idea …
EDIT – I suspect by "hump" you mean the old riser that is sticking up from sea bed … I would attach a cable to it before you cut teh old riser … have it attached to a crane on surface and winch it up once cut loose
220mph,
That hump is about 3,000ft of riser the center of the hump is 1,500ft off the seabed. It’s full of gas and oil and has flotation collars on it, that is why it’s floating.
There is a lot of speculation on the flow rate. The only way it matters here is to help weigh the risk of doing something against the risk of waiting.
Procedure for measuring the flow:
1) look at the film and see if you can track any significant features as they exit the pipe and track accross the frame.
2) Measure how fast they move in pixels per frame.
3) Go find the ROV and on the surface, use it’s camera and the end of a similar piece of drill pipe to set up the same picture.
4) Insert some yardsticks in the pipe and take a picture. You now have a scale to convert pixels to inches with corrections for perspective.
5) Use above to make multiple mesurements of the outside velocity of the flow.
6) Compare the results.
7) Go find a fluids person and decide on the likely range of flow profiles at the mouth of the pipe.
8) Calculate a range of the possible flow rates from above.
If someone published the results of each of these steps, it seems we could have an auditable estimate of the range of pissible flow rates.
From the information the house released, does it look like they were pumping mud down the hole just before the end. If they knew they had a kick, would they have closed the annulars. (This appears consistant with the survivor’s accounts.)
If we agree that the annular is closed, maybe the state just as the platform sank was:
1) Annular closed with drill pipe extending from sufface to 3000+feet below sea floor.
2) Shears not closed either because they weren’t asked to or couldn’t.
3) LMRP not disconnected because of the drill pipe.
(Either din’t get enough tilt to trigger, or did trigger and drill pipe held it together.)
Which leaves us with the flow mostly being held back by the kink in the drill pipe. (Fortunately, BP sure buys good pipe.)
If the kink is working for us, what if we try to make it work a bit better. What would happen if they rig some cables on the riser a bit up and down stream from the kink and haul the two halves of the pipe a together a bit.
I know it’s risky, but so is the continued flow to the Gulf. I would certainly try it somewhere else first. Maybe see how strong the pipe is after kinking. We already have one test case, it looks pretty good from the original event.
If they get good at measuring the flow rate, then they could pull a little bit and see what the flow does. (Or use the flow rate to figure out how much the pipe is kinked?)
After reading what I wrote, it seems a bit like the cartoons were the character trys to fix a sink and ends up with a flood, but maybe there is something useful in the idea.
Maybe this time the cartoon character gets lucky.
Just heard from engineer working for BP that they will try junk shot today, then top kill if it holds. See my comments from before for more details of these procedures.
I have seen videos like this one – http://www.youtube.com/watch?v=PX08ajQP8Mk&NR=1 showing some dark material and some lighter material coming out. If the dark stuff is the oil, what is the lighter coloured stuff – tiny gas bubbles, a solution of gas in water or what?
If the light stuff is gas bubbles at 150 Bar, and the gas-oil ratio talked about here is 3000:1, does this mean that only about 1/20th of what is coming out of that pipe is crude oil or is it not fully separated?
What is happening to the gas – is it dissolving in the sea water on its way to the surface or it is forming an inverted cone of less dense water – an obvious sinking hazard to surface vessels?
How about using a bigger pipe over the end of the 21” pipe? Iknow it would freeze up so use hotnsi’s bag to seal the end . it would be trying to syphon the water around it ? Im just asking . I dont believe that would disturb to much of the riser and shouldnt put to much mor pressure on the riser.
AIEngineer,
The pipe the large leak is flowing from is broken off riser, it’s kind of pinched from bending over and snapping off, but since it’s not full flow across the whole pipe so that doesn’t matter. Only the top 1/16th or so has oil and gas in it.
So the hole size is 18-3/4" ID
As far as the LMRP not unlatching, just before the initial explosion the generators had shut down and cut power, this would have also shut down the station keeping thrusters. By the time they decided hit the panic button the rig may have drifted too far off center to allow a disconnect, or the LMRP was already in too much of a mechanical bind to to do so. Most of this equipment is design to function properly when everything is vertical, and centered over the hole, but will still function within a given design envelope. If conditions are outside of that envelope, the odds of a malfunction are greatly increased.
I can pose a theory here, that when the riser filled with gas, that the lower sections of riser collapsed, pinching the drill pipe, and with the pipe rams and annulars closed, even if the latches had disengaged the LMRP couldn’t detach from the stack. Also depending on how the deadman logic was programmed it may not function if the annulars are closed.
It would be interesting if they could get an ROV to check and see if the LMRP connector is still latched now. I don’t know about this particular LMRP connector, but the ones I have seen have a tattle tale flag, this pokes up next to the hydraulic connections to show if the connector is latched or unlatched.
OldDiver,
The gas cut is 3,000SCF/bbl, that number is based on atmospheric conditions, ie 14.7psia and at 60degF. Without knowing the physical and chemical properties of both the oil and gas, how much is coming out of solution at the seabed would be, pretty much impossible.
Plus if you watch the tape for a while you can see it surges from oil to gas and back again to oil and the flow rate surges as well, that is caused by the 1,500ft hump in the floating riser.
Horizon 37 do you understand my question ?
I’m not H37, but a bigger pipe (and why do I think 21OD drill pipe is the largest standard size?) would be 5-6 times more massive, have several time the cross sectional area, and would be therefore a great deal harder to handle and keep stable.
If a 6inch pipe is big enough to transport the leaking oil to the surface, then it would make sense to use it. No point in using something larger and harder to handle if it isn’t needed.
hdbob, kenbobb,
I don’t really know what they hope they can do with that 6" pipe, the oil and gas are flowing along the top of the riser, they would have to find a way to hold it up in the oil stream for it to be of any use except for sucking up seawater.
If they could clear out the blockage of the larger cofferdam and re-deploy it with the pipe to surface already installed, they could run a deepwell pump down it and pump the oil up as opposed to letting it flow up on its own. One of the secrets to fighting hydrate chunk formation is that if you can keep it moving it won’t form chunks, it just stays slushy. And if they inject methanol into the top of the cofferdam it will help keep bergs from forming there.
Horizon37, hdbob, kenbobb: If they blocked the riser downstream from the end of the 6" pipe, wouldn’t the pipe pick up oil and gas? Wouldn’t the seawater in the pipe soon be all pumped out, and then the 6" pipe would get just what is coming out of the well?
Using a 6" pipe instead of a larger pipe over the riser, would keep the oil/gas mixture flowing at a much higher speed, inhibiting hydrate formation, as H37 says above.
Has anyone heard if the Top Hat worked?
I keep wondering why they haven’t retrieved the caisson and cleaned it out, readyiong it for redeployment if the Top Hat works.
TMM16,
BP is going to try their 6" pipe trick before they deploy the "top-hat" rig.
Personally I don’t give the 6" pipe thing more than a 10% chance of working but they are trying.
From the video, I think I’m seeing the end of the riser.
If the oil is coming out of the drill pipe,
it looks like the end is pretty far up inside the riser.
I wonder how far the drill pipe slid down into the hole when the platform let go.
(Would the annulars have been able to hold it up)
It looks like the riser is a respectable gas/oil separator.
Maybe they could take advantage of this by taping the top of the riser back from the end and letting most of the gas out. This might help the hydrate problems.
my solution
[http://www.flickr.com/photos/23462826@N07/4607736206/]
explanations here
http://www.proinvention.com/BP.html
You fix a jaw on the pipe
1. Jaw have pivot for putting level with half of cap
2. You push the level with a jaw for example and so the half of cap close the end of pipe
3. After closing of the 2 half o cap, we put a second complete cap on the 2 half of cap
* If the leak is at the middle of the pipe, device work with half of cylinder at the place of cap
* we can set it at the top of the bop at the place of the rise with some horizontal levels.
* At the top of the half of the cap, you can add a device for connecting another tap an rise
You can have a set of jaw connected by cable
Here there is a set of 3 jaws
In this manner, you can set the device on a curved rise because of damage
Of course you can set a jack at each side of the device (Jack is not showed here)
Half of cap can be replaced by a half of cylinder in the case of leak at the middle of the rise (not at the end)
Half of cap is not really at 90° but 89° because of the join compression setted on the section of the cap
Etc….
Hi, here is a sketch of my proposal, the key point is the use of a soft material such as a textile, fabric, or PVC for the tunnel and funnels, the most suitable material should be chosen, I don’t know which one is best. It would be lighter, easier to install, cheap, and less sensitive to ocean currents. Once secured to sea floor with anchors or ballasts, it should work fine. The petrol can be pumped directly from the surface.
http://www.flickr.com/photos/caresma/4607819794/sizes/o/
AIEngineer,
From the layout of the riser on the seabed and the fact that it’s pretty much intact (only broken apart in one place) it probably stayed attached to the rig until the rig was over halfway to the bottom. It’s pointing right in the general direction of where the rig is lying on the seabed. In other words I don’t think it dropped in the sense that some might have expected. I have seen pics of dropped risers from drill ships and semis and they are all busted up with pieces of riser scattered all over the place, flotation collars knocked off and floating around on the surface … a Big Mess. From some of the USCG pictures of the rig while it was sinking you can still see the riser attached to the rig, although the slip joint is detached and melted over like a candycane, the tensioner wires are still holding the riser up.
And yes the annulars will hold up the drill pipe, another name for them is spherical BOPs because of the way they function, you can think of them as big half rubber balls with steel fingers on top and a hole in the middle.
They work by a hydraulic piston pushing up on the bottom of them, the top of an annular is shaped like a hemisphere inside, so the piston pressure from the bottom squeezes the hole in the middle closed. The harder the tool joint on a pipe pulls downward on a closed one the tighter they grip it.
That said I don’t think they were the only thing holding the drill pipe, I am pretty sure the riser was collapsed on it pinching like a pipe vise.
If you refer to the videos of the leak, that is what a broken riser looks like that gets bent too far, the riser at the LMRP is not snapped off like that so I think it was collapsed first and that would allow it to bend over instead of break off. A flat strip of steel bends a whole lot easier than a tube.
i will agree the the speed will be greatly increased in the 6 "" pipe. I dont believe it will handle all of the flow or even a third of it . Im not trying to tear off the arms and legs of the baby doll . A short piece of pipe ya its heavy were not looking for long term or to put a valve on it just get it to the surface and have it loaded in a tanker , barge or what ever . it should keep the water out and help with the ice crystals formation. The dam would let the water right in underneath it and help the hydrates.. Shoot me down. just got off work.
The 6" pipe with a stopper … I call it the "straw and stopper" has a crucial problem … several in fact …
The biggest problem repeated here is the worry about the structural integrity of teh old riser … that first, even undamaged it is only designed for a fraction of the well pressures … and second that with in crunched, bent, kinked etc … and already having several leaks ( ie: at the kink at top of BOP) that any increase in pressure by capping would risk destroying/blowing the
Adding a 6" line with a stopper is reducing the flow from 19 5/8" to 6" … there is a high risk pressures will significantly icnrease in the line risking a catastrophic failure
Additionally they will have to operate direct IN the oil and gas plume to accomplish this … the ROV’s will essentially become blind it would seem – and wiothout video they cannot be operated
Last – by its nature its a kludged operation – they are working in a damaged, ripped, open pipe end …. there is no way to enginerr or design a plug – it has to be elastic … something like an inflatable plug – but with a hole in it for the 6" pipe …. this "plug" will have the full pressure in the pipe acting against it
My design – the hot tap – avoids all of these issues
… it first creates a safe, sturdy, stable platform and fixture to operate from … second it isolates the operation from seawater
…. next it never risks increased pressure in the line – it installs a pressure relief – the full size new riser on the forst tap port – before any attempt to cap …
… it isolates the oil and gas from the tap and cap operations – so the ROV’s can "see" to operate …
… it operates on undamaged riser – so fixtures and attachments can be realtively easily designed for a good fit
…. it uses standard off the shelf components – valves, pipe etc …
It is extremely simple and relatively permanently solves the problem … once in place it is unlikely to fail (compared to the stopper and a straw which could fail any time)
It allows a number of additional ports to be installed in the riser line – telemetry ports, hot water, methanol, CO2, chemical dispresant etc ports
I honestly cannot believe the best these "experts can come up with is this "straw and stopper" idea … which has all of the problems identified in this thread – and IMO a very low likelihood of success
BTW – not advocvating my idea becasue its mine …. only care that if it could work it be used – to stop the leak and damage
220mph,
Here is BPs graphic of the 6" suction pipe,
http://www.piersystem.com/go/doc/2931/551107/
As I said before I don’t give it a better than 10% chance of working, because they have the pipe centered in the riser, the flow in the riser along about 16% of the top their pipe needs to be off centered to the top of the riser.
Here also is a graphic of the relief well progress.
http://www.piersystem.com/go/doc/2931/551163/
I would also use as noted the failed "outhouse" containment box …
Sink it in the mud close to the install of my hot tap saddle … attach an arm to the bottom of the contaiment box and attach to the Hot Tap saddle to support the saddle and old riser pipe end
… install a piece of new riser pipe from the hot tap lange a little taller than the conatinment box … add another arm to top of containment box and attach to top of this short piece of new riser pipe … add an annualar – a spherical BOP using Horizon37’s term – on top of that short riser pipe – and attach new riser to surface to that …
In essence the hot tap saddle, and short riser pipe and annular, becomes the new "stack"
This new "stack" is supported and stabilized by the containment box sunk in the mud next to it (like a rocket gantry) …
Horizon37 …
Welllll …. they do draw a prettier picture than I do ….
And I guess we shouldn’t call it a "stopper" … more a "flapper" ….
The good news is it probably won’t increase the pressure in the pipe – since it doesn’t seem likely to be able to hold back anything – looking at the video of the velocity of the oil and gas exiting I see little likelihood something like what is shown will have any real chance of stopping the flow
I also don’t really get the nitrogen bit …. they already have large quantities of gas – which certainly appears to rise rapidly in the sea water … if the inject nitrogen into the riwser its just gonna get blasted out past the flapers it would seem – with the oil and gas …
I suppose they could inject nitrogen down toward end of the new pipe but not into the riser pipe – hoping as that nitrigen raced back up the new 6" pipe to surface it would create a suction …
Not only do they try and take oild and gas from a 19" pipe and shove into a 6" pipe but they also have largely pre "kinked" the 6" line ….
What’s your take?
I believe I could have personally fabricated my entire HOT TAP saddle fixture in the time it probably took them to draw that picture …. … and then they’d have something a lot more likely to actually work
I suspect they think the oil will somehow pool behind their flappers while the gas escapes thru it ….
Their system also appears to require an ROV to permanently stabilize it and hold it in the end of old riser … I suspect that small arm is supposed to be some kind of clamp but judging by the video of the flow of gas and oil I would ssupect the ROV would be unable to see to secure it to the pipe
Looking at the drawing showing the relief well progress I was reminded of something I read about the Timor blowout off Australia.
If took 5 attempts to drill the relief well. One of the problems indicated was binding due to the curvature required to intersect the blown well.
Does anyone have knowledge of the strata they are drilling for this one? Is it favorable, difficult, unknown?
When I look at the drawing, I see they are aiming for an intersection at 18,000 feet. Why so low? Is it to generate a larger static head? Is it to get below suspect casing?
Junk shot readied.
http://www.nytimes.com/2010/05/15/us/15junk.html?pagewanted=2
Hopey hopety hope.
Time to shut this motherf*****r down!
Hey, 220MPH, I said I liked your idea!
I also think it makes sense to relieve the pressure on the pipe outlet before sticking in a collector pipe, but what do I know?
Another thing I think is that they should have a small pipe that will allow them to inject methanol or glycol into the stream to dissolve any hydrates that form. Hydrate formation seems inevitable, given that what they seem to be proposing won’t be water tight (at least if I am following the graphic correctly).
Will it get all the oil? Who cares! Get some of it. Although it does beg the question–will a 6 inch pipe (subject to at least some hydrate clogging) be enough? And would it have been so much harder to use a 10 inch pipe instead (which would have had 2.5 times the cross-sectional area)?
I suppose the engineers working on this know how much pipe they need to manage the volume, but I hope they don’t feel duty-bound to honor the widely disputed figure of 5000 barrels per day.
Rough calculation. A cubic foot holds 8 gallons, so a six inch pipe (27 inch cross section) contains a gallon every 8 inches. 210,000 gallons a day (if the 5000 bbl/day figure is right) means 1,680,000 inches of flow per day. Thats about 28 miles (oops, didn’t fix this the first time) per day of flow in the pipe, or just less than 1.2 mph flow rate (just over 0.5M/sec).
How does that flow rate stack up in the real world? What kind of pressure differential is required to create it?
1.2 MPH is a slow walk.
Everything get multiplied by the actual flow rate, so if we’re really seeing 10,000bbls a day, we’re moving at a brisk walk. 40,000 a day and we’re running at a good clip.
Are we asking too much of the pipe?
P.S. I screwed these calculations up twice, so I hope I finally got it right.
Last note for the morning–thanks again for the expert commentary from just about everybody.
Sometimes my head hurts trying to figure out what you’re talking about, but eventually I end up quite a bit wiser.
Very nice diagrams posted today as well. It really helps to be able to visualize the situation.
Several days ago I sent this in to BP. I think it covers most of the basics, but any success in Deepwater is the product of the input of dozens of smart people:
RISER END TO SHIP IDEAS
Flow from the riser end will need to be restricted and funneled into a production riser that connects to a surface vessel that will have separation and storage/ offloading capabilities. That will require something tubular and of a semi-elastic, non-reactive material placed on the outside of the riser and clamped down to direct the flow into some flexible pipe (coflexip) of a diameter that will not cause excess back pressure to burst the riser at a weak point. Care should be taken to provide flexible internal armoring for the sheath, especially the part that will contact the end of the riser, as there may be some sharp and jagged areas that would come in contact with the semi-elastic sheath. [The flexible pipe part of this will always require sufficient cables attached and tensioned to keep it from flopping around and damaging itself during installation and when the oil is flowing through it up where it is firmly attached to the structure.]
Installing the Sheath
To get the sheath around and secured to the pipe without creating excess back pressure on the damaged riser will mean that the back end of the sheath/ coflexip/ containment structure will need to be free of obstructions, so there are several large vents (more later) to remain open as a shunt for the oil during the installation process. The sheath will need a rigid, bell-shaped mouth (perhaps with the bottom modified/ shaped to deal with obstacles on the riser/ ground interface) to aid in placement over the riser. On this there will be attachments for four guidelines to pull this over the riser mouth while controlling the motion as the force of the oil being expelled from the riser will need to be managed.
The pulling could be accomplished by some type of winching devise attached to several heavy objects (i.e. well secured) lowered into place to do this, placed ~20 to 30 feet behind the riser end. As the mouth of the sheath approaches, the oil flow will be pushing the mouth upwards and sideways, so the will need to be two of the guidelines at the top of the sheath mouth with the ability to pull downwards while the other two provide the lateral pulling power to get the sheath pulled over the riser, maybe at a 20 to 30 degree angle to help the lateral stability. The sheath will need to be pulled over a long enough portion of the riser to allow a clamp (or several) attached around the sheath to be closed enough to eliminate oil flow out (or water in) and reduce any movement of the sheath that would endanger the sheath’s long-term survival. This may not need to be more sophisticated than a large version of a garden hose clamp, permitting an ROV to screw down the clamp(s).
Flexible pipe to receiver to production pipe
Going from the riser end the flexible pipe will need to be attached to a structure that is 1) stable and heavy enough to withstand the vertical and lateral forces exerted by the pipe connected to the surface and secondarily whatever forces the oil flowing in the flexible pipe that will be attached to it generates, and 2) provide an adequate seal to minimize the water entry that leads to hydrates and emulsions.
The structure, which can be a box or cylinder as long as it is adequately stabilized by sufficient mud flaps or the equivalent shaped base, will need to have an adjustable set of cables to hold the flexible hose in place once oil begins flowing through it, but allow enough movement for the securing of the other end over the riser. The structure can then have the flexible hose connect to a similar or somewhat larger diameter pipe or even a small chamber that has several large open (but sealable) vent ports, maybe 16-inch diameter, to keep the oil flowing out of the structure (the piping roughly shaped like a “t” or even 4 opposing vents, but the simpler the better), but keeping the back pressure exerted on the riser to a minimum, until the fluid coming out of the riser has cleaned up to only oil.
This structure could have as many instruments built-in as needed; pressure gauge, flowmeter, injection ports for methanol, etc., to monitor the situation and provide for flow assurance needs.
The outlet at the top of the structure should be a mounted Subsea FlexJoint, or its equivalent as on a BOP/LMRP, on which the production riser will be attached. This will allow the tensile and lateral forces to be safely dealt with during production and permit easy connection/ disconnection options.
With the fluid cleaned up, an appropriately sized pump (progressive cavity or ESP) near the bottom of the production pipe is started up as the open vent ports are closed to keep the amount of hydrate slush to a minimum. At this same time a large injection from a reservoir of methanol located in the structure should be flushed into the steam of oil/water to reduce the chance of hydrate initiation during the changeover period. Hopefully at that point the fluid can then be safely pumped to surface separation and disposal.
Stabilizing the production string
The riser will have to be able deal with changing currents at all levels of the sea. That will require some stabilization. I propose that numerous attachment sites be placed on the riser 400 to 500 feet above the bottom, and again at 1500 to 2000 feet above the bottom (SWAGs, a riser hand with a computer program could improve these depths in short order). These would be some type of quick connect/ disconnect that would connect to cables, on three side of the riser for stability (i.e. about 120 degrees apart). The reason for numerous sites would be to make sure that a connection point would be available for each cable, and getting the exact length correct would be extremely unlikely in a hurried situation like this.
The cables would then connect to weights several hundred feet out for the lower connection points, maybe a thousand or more feet out for the higher connection. Taking an old trick from early in mooring offshore structures, and easy to construct in a hurry, would be a series of weights to provide increasing tension for the riser as it gets pushed away from the weights. The weight farthest out would be very heavy, say 30 or more tons so it would not move no matter what happens. The next weight, connected by a rugged cable, about 15 to 20 feet closer to the riser would be on the order of +/-7 tons. Then attached to it a weight of 3 tons. Then another of 2 tons. And finally a one ton weight. These would provide increasing tension as the riser is pushed away from the weights and they are raised one by one. [A mooring hand could quickly improve on this].
The rig should be able to provide sets of lines attached with the appropriate tensioning to keep the upper part of the riser from dangerous movements. But that part is similar enough to a floating production vessel that it should be simple to copy from a similar sized riser on a floating production unit.
junk shot diagram
Thats junk shot is cool as long as it stops it up . It could also erode out the valve or stop up the riser at the crimp. Then what ?
What side of the world are you all on its 9:30 pm here.
Yeah what it is going to stop up, is the choke and kill lines, screwing the pooch for the next guy that wants to hookup the BOPs, after the well is killed by the relief wells. Dumb Idea
And there we have it. Horizon does want to have the oil leak continue. What could be in it for some people to have the oil continue leaking. more eco terrorists involved in this than meets the eye. I have been wondering why the junk shot hasn’t been done yet. It should have been one of the first things tried. It will work if done right and you all know it. what they have been screwing around with all this other crap for is hard to figure, unless intentionally trying to cause more damage .
What group is it you guys are with and what did you pull this crap for? What could be in it for you?
Hammer,
You’re in fine form tonight, I don’t want the spill to get bigger.
I want them to do something that will work, this won’t!! if it plugs the crease in the riser it’s flippin game over pal.
Because that riser will burst and the only reason it hasn’t yet is:
a) the well is flowing, and gas is not accumulating in the wellhead to increase the pressure.
b) it’s already collapsed and to burst it it has to expand.
I gave them plans on what to do, the day after the rig sank. And these plans have worked in the past in the Arctic Ocean, a heck of a lot colder than it is at the bottom of the Gulf and they worked in 1,000ft of water.
The parts to do it with are on the ground and nothing has to be fabricated. All they have to do is send a C-130 up to Tuktoyaktuk, NWT, Canada to get it.
It’s a steel umbrella shaped wellhead cover, it’s already in segments strapped to C-130 Cargo Pallets all they have to do fire up a forklift and load it. It fits on the bottom of a marine drilling riser and the Discovery rig has 12,000feet of it on-board. It has methanol and gas lift lines already in place, as well as water jetting lines if it happens to get stuck in the mud. it’s 40ft in diameter so it can be placed well above the leaks without endangering any other equipment. And there’s 3 of them just in case they lose one.
sounds exactly like the "umbrella" design I envisioned … a pipe with an umbrella at top … the umbrella framework unfolds much like a real umbrella … the "handle" of the umbrella is simply an anchor to attach to the pipe at the leak … oil rises and is vcaptured by the umbrella – which has a connection on top to connect a standard riser pipe – with choke, kill etc lines that can be used for methanol. CO2, warm water or whatever is necessary to keep oil flowing
It can be lightweight – even possibly some kind of fabric … even if it didn’t exist it could be fabricated fairly quickly …. even if it didn’t work there is no downside
And I completely agree on the junk shot deal …. they KNOW the shears/rams in the BOP stack are NOT closed – that oil and gas are passing – and in signiofciant amounts … they also know the choke and kill lines are small – I think you indicated 3" or less – which limits the size of material they can shoot thru them …
And some or all of that material IS going straight thru the BOP stack and to the kink … where it is visually very clear there is a very low "height" in the crushed pipe … the junk kill will almost certainly as you note NOT Pass thru this very narrow vertical height opening and will indeed work – it will junk up the RISER at the kink – subjecting the already heavily damaged and leaking riser to more than enough pressure to blow it wide open …
The positive is that will force them to simply unbolt the damaged riser – as the well head will already be exposed to the sea – and then try to bolt new riser to the stack … now THAT will be a real challenge
and who woulda ever thunk it? that a "Hot Tap" might be a possible fix …. yeah! thats it … a HOT TAP ! … thaaaattts the ticket!
😉
Plan D: The "hot tap."
BP’s Backup Plans: From ‘Hot Taps’ to ‘Junk Shots’
"Plan D: The "hot tap." Engineers want to tap into a section of damaged riser and suck up the oil before it can travel farther down the pipe and spew from the large gash.
Amazing …. weeks later …
Probably just coincidence but I emailed the drawing above 2 days ago directly to the BP team …glad to see it finally considered
What is you opinion on this proposal ?
[http://www.flickr.com/photos/23462826@N07/]
wen can add notch for the drill pipe
[http://www.flickr.com/photos/23462826@N07/4607736206/]
hountsi,
It’s a good idea, but you need to scale it down some.
It’s a 21"OD Riser Pipe that it has to clamp on to. And it’s laying flat on the seabed. Possibly make the legs shorter and use hydraulics to open and close them.