Posted on
May 17, 2010 by
bp complaints
New Deepwater Horizon images:
ROV attempting to activate Deepwater Horizon Blowout Preventer

Image by uscgd8
100421-G-XXXXL-_003_-_Deepwater_Horizon_fire

Image by uscgd8
Deepwater Horizon Oil Spill – MODIS/Terra Detail (with interpretation), May 1, 2010
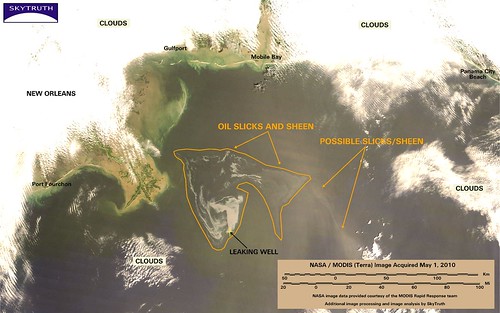
Image by SkyTruth
Tags: Activate, attempting, blowout, Deepwater, Horizon, preventer
Category
News
Trackback: trackback from your own site.
BP can easily be compelled to release the documents by a grand jury, and there is nothing they can do to block it. It won’t come down to that; it’s in their interest to cooperate, but surely they are waiting for the requests to come through official channels. The official channels are waiting for a compelling reason to make the request.
BP’s lack of of protocol for loss of control coupled with their failure to gain control will not stand for too much longer. Obama is already assembling a team that is seeking out people to augment BP’s efforts. Certainly they will have access to anything they need from BP whether BP agrees or not… but they will.
Even though retired now for Eand P management I would assume between BP , their partners, and the service companies they have contacts to every major university and expert around the globe. Add to that governent agencies and the fact BP has already stated they are using Sandia National Lab technology to try to find out the actual internal condition of the BOP before trying the junk kill, indicates that government experts are in the loop. The administration is going to say what they say and the hearings now are the accepted political grandstanding. Now perhaps there is some Defense Department or CIA expertise we do not know about (Howard Hughes is dead though so no Glomar Explorer).
In both hearings today all parties have said information will be released as soon as practicable. However, in all disasters (or even wars) I know about, no response or action is ever good enough. Unfortunately, either folks will pretend we can eliminate risks or on the other hand say that if we cannot we should not do whatever we do.
Sadly, knowing some of the individuals, it is sad to see the accusations of "evil" and insensitive being thrown at them.
DelShady,
Yes a Grand Jury can compel that documents and witnesses be produced, but they can not release them to the public, they would be used only in a Grand Juries formation of an indictment, and this is a civil case so No Grand Jury.
The proceedings of a Grand Jury are secret, the police nor the DA, AG etc. may interfere with them, a judge may be called in for enlightenment of the Jury on a given law or to get subpoenas for evidence, but may make no instructions unless asked or interfere.
oceangopher,
I doubt if they will try to recover the whole rig, nothing of that size and weight has ever been attempted at 5,000ft, not to mention it would probably take 2 years or more just to plug enough holes to get it to float. And the expense would probably be more than a new rig. They may get some of the submersible and manned gear from the French, that they used on the Titanic to poke around inside the rig, only time will tell on that one. They may do a hot tap on the fuel tanks and what engine oil tanks they can, to recover the diesel and motor oil before it starts floating out and making a slick. The Horizon could carry up to 700,000 gallons of diesel, it will be known from morning reports how much fuel, oil and other bulk materials they had on board at the time.
"However, in all disasters (or even wars) I know about, no response or action is ever good enough. Unfortunately, either folks will pretend we can eliminate risks or on the other hand say that if we cannot we should not do whatever we do."
I just want to know the events leading up to what happened, and a good summary of what is currently happening.
I don’t personally feel like we’re getting that.
Horizon37,
Outstanding info from you, B.T.W.
Yes, I doubt the documents would be publically released by BP, but the info will become available to the government unless they get this under control soon. It’s too bad, too; people such as yourself should have eyes on that data, but it could open up a PR nightmare.
Some very smart people will be put on this, and once mandated, they will swing their giant brains on the problem for a good look. Some may not even realize yet that they have the answer.
Dick Feynman himself pinpointed the cause of the shuttle disaster, and I doubt he would have even thought about it if not on the commission.
BP could possibly be working against themselves right now. My gut tells me that if the riser were to give out today, that all of a sudden more options to cap would open up. In other words, they might be unduely hesitant about increasing the flow even though doing so might give them more options for gaining control.
It’s a classic problem in everything from trama centers, to the Federal Reserve.
thanks Horizon37
how would they expect the cofferdam to "contain" the flow and allow it to flow up some drillpipe? would it not have to be pumped?
Let me also chime in with appreciation for all the knowledge Horizon37 brings to this forum.
I struggle to comprehend it all sometimes, but I feel like I have a much better grasp of the general outlines than I used to.
Other folks who have shared their actual experience please also accept my gratitude.
Assuming the hanger locking rings were installed, it sounds unlikely that the hangers for the production liners are blocking the shear rams. If there was no cement plug, then is sounds like cement in the shear rams is unlikely also. What does that leave, except for the drill pipe?
Hopefully the folks at Sandia can figure out a way to find out without frying the electronics we need to do something with the information.
Two things still boggle my mind in this:
1) The idea that it’s ok to have a ‘failsafe’ BOP which has a percent or so chance of not working (2 feet unshearable pipe joint/100 foot pipe section is not failsafe in any industry that I know about).
2) The idea that with computers all over the platform, they didn’t have a filesystem backup server near the exits so they could take it with them when they abandoned ship.
I guess the Exxon lesson was doubled hulled tankers. Maybe the BP lesson will be to fix something like the above list.
H37: Wiki says the 5th Ammendment also applies to civil cases, so it must be true ;-). Unless something overrides this, we need to figure out how to convince BP that it’s in their interest to talk.
"2) The idea that with computers all over the platform, they didn’t have a filesystem backup server near the exits so they could take it with them when they abandoned ship."
Considering all the truly pertinent data for a month could be logged on an average flash drive installed in the lifeboats, it seems like a very good suggestion.
Also, maybe a "black box" that get fired off the rig with a sonar pinger and a float? Compared to an aircraft, this kind of documentation seems rather trivially easy. We should be doing it.
Also, look! We made the New York Times!
At least the photo at the head of this discussion did….
http://www.nytimes.com/2010/05/11/science/11blowout.html?hpw
The story included seemed far less stupid that most of what I’ve been reading lately, however.
Maybe a reporter didn’t stop at the picture, and actually read some of the comments?
HORIZON37 … another couple questions/ideas
We have seen the pictures of the appx situation on the bottom and the leak(s)
farm5.static.flickr.com/4067/4581515175_0763849555_b.jpg
The pictures show the lak at the kink above the BOP to be a very minor leak … the main leak is the far nd it appears – or at least well out in the riser … at the leak point the riser is laying on bottom of seafloor (this is where the outhouse was attempted to be placed)
presumably there must be sections of the riser pipe relatively undamaged in that area
… why not use my HOT TAP method to tap the pipe at this point – in an area closer to BOP than the current leak – as close as you can get with pipe still in a stable position on sea floor
… use two taps or my "double tap" design
… something similar to this:
http://www.teamindustrialservices.com/taps/images/hot_tap_pic.jpg
… first place a hot tap, with a gate valve … drill the riser pipe thru the gate valve, close the gate valve remove the drill rig and attach a new temporary riser pipe to the surface … then reopen the gate valve so oil can flow into new riser pipe
Then use the second HOT TAP … drill the riser … remove drill rig and bolt on a ram type gate valve that blocks the riser pipe … doesn’t have to block completely … may even be able to use some kind of inflatable or expandable plug especially if it can be anchored ….
This lest the riser be largely blocked – with no real risk to integrity of riser as the "bleed tap relieves any pressure due to blocking the riser …
Once flow is largely blocked cut off end of riser and cap
At this point you can cut out the major leaking section and any oil making to that point can be evacuated thru temporary riser to surface … there is no pressure increase as the new riser connection should be a larger opening than the leak – if anything it should reduce pressure
If the small leak at riser is not leaking significantly at present – and pics appear to show it is not … this capping as long as a relief pipe is inatlled should not change that
This should largely conatin the leak at least temporarily
The next question … once there is some kind of connection giving access to the riser pipe why couldn’t drilling mud be pumped thru it back into the well to displace the oil?
If oil can make it thru the kink and the BOP stack then mud should be able to make it thru the other direction?
Even if the mud doesn’t workat mimimum the hot tap and capping of riser pipe I note above should capture the oil leaking and give time to complete the new well drilling …
220mph,
I sincerely hope they don’t mess with that riser until the well is killed, or at least until they know the pressure inside it. Disturbing that riser would most likely cause the small leak there to become much larger, you have to remember it didn’t start leaking until the day after the rig sank, that indicates that the steel there is under tremendous stress, attempting to punch a hole in it may cause the crack to grow, or for the kinked area to fail completely.
The leak there may be a small crack under high pressure (Most Likely) or a fairly large crack under low pressure (Not Likely).
Doing a top kill requires injecting mud at a higher pressure than it takes to flow the well, (It has to force the oil back down the well) this added pressure could also cause the riser to fail, this pumping procedure is called "bullheading", since there is no way to close off the well head and use a choke to bleed off pressure wile injecting mud and waiting for it to fall 18,000ft to start building up a mud column bullheading is the only other option, and it takes a lot of pressure. The best option is to leave the wellhead alone, develop a method to get the oil to surface that works, and wait on the relief wells to do their job and kill the well from the bottom up. At least if they start killing the well through the relief wells and the riser fails under the added pressure, they have 2 rigs there to fill the hole as fast as they can pump into it, killing it before a spill from the failed riser becomes too great a mess.
In case you didn’t see it here is a side view of the riser.
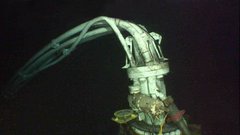
We have a dripping faucet. Messing with the kinks in the riser brings the risk of making it a flowing one. It seems like tapping where the riser is laying on the sea floor, not under stress may be low risk. But when you connect a pipe to the surface, if that pipe moves around it might apply force to the riser which comes with risk.
If they could figure out a way to not apply force, then that tap might be a good place to inject something to prevent the ice formation.
I wonder if they have thought through what to do if we do end up with the flowing faucet. It would be ashamed if they have to start the head scratching after it happens. Perhaps being ready to cycle the BOP in hopes that the trash will flush would be a prudent.
In yesterday’s hearings, I think I heard BP say that they had a server on land recieving status from the platform in real time and that the USCG got a copy of these. If this is so, then perhaps FOIA would help here. Or if they are available this way, then it might be smart for BP to preempt this with an information release of their own.
Horizon37,
Thanks for the great commentary. IMHO, like you, I think you can tell any option to kill the well is being wieghed against the best guess of current flow and the best guest time for the releif well. During the hearings yesterday senators challeged BP by saying they did not have a plan if the well failed. They used the current subsea attempts to say they are fumbling for solutions. As others have pointed out, a standard plan would consist of proven methods that would be to drill a relie fwell and concurrently to deal with the oil at the surface and cleanup. Infortunately by trying to find "new ways" to stop this unique situatiion and to demonstrate they are not just sitting around waiting for the relief well has kind of blownup in their face with accusations they should have had containers etc. ready. As BP has said it was not only frustrated by the BOP not shutting completely as they had intially thought, but also they did not expected the riser not to disengage at the time of sinking.
I go with the idea that the probability of a junk shoot /top kill to not ppen this well to full flow has to be high. 60 days more or so (about) at 5000 barrels a day might be a lot better than 50000 for even a few days As with dispersents and prioritizing boom placement locations you have to weigh all alternatives. Imagine if a top kill or something else increased the flow. If there is a PR nightmare now, it would be orders of magnitude greater. You have to know that Salazar et al are not going to apporave anything that would could it worse.
As an aside after watching the hearings I find it amusing that all headlines try to summarize them as folks trying to pass blame. In fact as many senators pointed out, having hearings now , before investigations have finished, is for theater. No matter how many times BP said as operator they are responsible for cleanup and for stopping the leak they kept asking who would pay. All three stated emphaticallyy that they had not finsihed investigations. They also only stated a few facts such as the cement job had been completed 20 hours earlier, Transocean owned the BOP (people keep acting thugh like they manufactured it). It is imortant to remember that any words anywhere near specuation at this time would be used against attorneys for both those killed and those trying to find legal negligence. As the BP America prez said there is the legal liability issues around the blast and BOP sitting on one side and the cleanup and economic cost issues on the other. It is alwasy funny though to watch the pols in these hearings. At least in this one a few know a bit about the subject, whereas in the AIG or Goldman hearings and past energy hearing the pols are embarassing in their lack of knowledge and need for election sound bites.
(How many times have you read in the media that Transocean and Halliburton are BP’s partners? It is Anadarko and Mitsui (who also have to pay their share of the relief wells).
Horizon–love that riser picture!
220MPH, thanks for the excellent link to the diagram. It’s much better than what I’ve seen so far. Maybe somebody else posted it and I missed it?
I like your idea, (speaking as a witless layman, of course.)
Except I think great care should be taken not to disturb the kinky pipe.
So, first figure out how the pipe is being stressed. Maybe a few anchors to the bottom where it curves back up off the ocean floor after the kink in the riser. That "floating" section has to be subject to some major forces from currents and tides. So pin down the section on the seafloor to remove leveraged stress on the kink. For all I know, this is already done. Now our pipe doesn’t feel so stressed!
Then put a sliding gate on the pipe a hundred feet back from and above the leak at the end (where most of the oil is coming out). The gate would be a cylinder in two halves, which would be bolted together onto the pipe. It would have a big cutout on one side that could be closed with a swinging hatch or a sliding door, whichever the ROVs would find easiest to manage. A big cutout, larger than the ID of the pipe.
Use a shaped charge to punch a hole out of the pipe in the cutout. It could be pre-positioned as part of the gate assembly itself.
Now the oil is leaking out 100 feet upstream of the previous leak, through a hole that can be closed. It isn’t coming out the end, getting hydrates all over everything, and making it hard to see the work.
Use the ROVs to cut off the end of the pipe at the previous leak. Install a receptacle end, or just connect it directly to a riser pipe to the surface (or put the caisson over it, this time without having to worry about it getting all clogged up with hydrates while it settles). Connect lines from the surface to pump down warm water and hydrate solvents, while no oil is leaking at the connection. Maybe put a line to inject hydrate solvents directly into the pipe, just ahead of the connection or caisson. This shouldn’t be much harder than capping the first leak. When the caisson is in place, or the riser pipe to the surface is connected, pump down that surface water to get things nice and warm.
When everything is warm, fill the 100 feet or so of empty pipe leading to the gate with hydrate solvent, to avoid creating an instant slushy when the oil/gas mixture hits the water inside the end of the pipe.
Close the gate and the leak will resume through the end of the pipe. Which now has a warm caisson over it, and lots of available hydrate solvent that can be tapped directly into the flow. This would put minimal stress on the kink, since all the action is at the low pressure end where most of the oil is coming out. It would prevent most of the cold seawater/methane mixing that doomed the first attempt with the caisson. And it would allow for immediate mediation of hydrate formation with solvents, before the problem became unmanageable.
Go fishing!
Some of the ideas that have bounced around in my head.
1. Disconnect at first joint of riser past the float. Cut off the drillpipe if it is present. Connect a riser hose end adapted to mate with the riser that leads up to Discoverer Enterprise. Drill ship is on station for that purpose. The ship has the station keeping capability to stabilize position.
2. Connect riser connections to choke and kill to relieve back pressure while handling work comences on Macondome2 or a mid riser break intervention. This could be done while any exorcise is conducted to relieve some of these stresses.
3. Preposition pull lines for disconnecting LMR from the stack. Same on other connections and peripherals. This would allow ROV to keep a distance if/when that first bend in the riser separates or some other reactions causes an escalation near the stack.
4. Stage the BOP stack on the Discoverer Enterprise with a full riser nearby suspended to facilitate rapid engagement during other recovery exorcises. The drill ship has dual blocks and rotary floor. This configuration could already be standing by.
My experience is limited and strictly on land. I am sure these ideas may be full of holes of their own.
Ok Bp has admitted the Bop had a hydraulic leak in the congressional hearings . I understand they are special fittings on the hydraulic line goimg to the bop . Why cant we cut the line and adapt some other fitting to try and close this thing it doesnt have to be done before how special is a coupling . Make it for the pressure required . what if it leaks hell we putting oil buy the barrels in anyway . Im sure the rov can do this.
All this speculation about what they could or could not do is an interesting intellectual exercise, but I agree with Horizon37 when he says he hopes they don’t do anything to the BOP until the well is killed. The risk of opening up the hole is just too great. In this case doing nothing is better than trying something so risky, which has such a high probability of causing a catastrophe.
Has anyone heard what BP plans to do if the top hat works? Will they retrieve the cofferdam and rig it with hydrate inhibiting devices like the top hat has, and try again?
TMM16, Agreeance! It does not sound like they will try it until they really have a good idea of pressures, what is going on inside the BOP stack, and a high comfort factor regarding success.
,
(Where’s Chuck Norris when you need him?)
So how viable do you think this new idea is?
http://www.deepwaterhorizonresponse.com/go/doc/2931/548915/
Also, here is a video of the oil streaming from the riser.
http://www.youtube.com/watch?v=WYFYVNvgg-A
BP’s "Top Kill" isn’t a "kill" in the "well control industry’s" sense of the word, yet a temporary shut off.
Everyone that understands this knows that there would still be a live well that has to be controlled; preferably from the bottom up. The relief wells would be enlisted to do this later.
I’m not posting the details involved to do this as I’ve noticed how quickly a dominant opinion in this forum, discredits the general concept of a "top kill" to shut off the leaks. Of course there are consequences that would involve solutions to them in the successful plan. I’m not typing more because, despite my IPhone’s many grand features, I’m not interested in getting into a "type off" with this group as I’m sure there is a keyboard in play amongst the most vociferous opponents of a "junk shot/epoxy pill/hot wax/top kill" temporary wellhead plug, in here. Not interested in one fingering against ten. I’ve been reading patiently in here while spending days on wells in a swamp with one bar cell reception, taking my eldest son who is interested in the energy business to a field where I’m flow testing a new well, at an event of oil execs in Houston, travelling to pick up my daughter from college and now on my way home.
Don’t be fooled by quick, erudite replies. Perfectionism hides behind false diligence, as it cowers in the darkness of it’s stifling delusions. We have a problem. A big problem and a problem with the integrity of the riser should an attempt at a "top kill" wellhead plug, plug off at the kink in the riser instead of inside the wellhead, where it would halt the leak. If the riser kink can only withstand 800 psi then the flowrate will increase only the amount that 800 psi increase across the sand face, using Darcy’s equation, will cause. Not an infinite increased flow, yet a precise amount that a petroleum engineer might calculate (unless lazy or distracted, etc.). This isn’t a plan stopper only a complicating possibility to be confronted with a solution. This problem solving process isn’t endless, yet demanding and unrelenting to wishful thinking nor passage of time.
Stopping the leaks to minimize damage before the bottom kills of a relief well will take skill and knowledge, of which, BP for sure has at least the second part; first hand knowledge of facts, yet do they have the leadership?
‘Perfectionism hides behind false diligence, as it cowers in the darkness of it’s stifling delusions."
Well, we might have you outnumbered, keyboard-wise, but dang, you can turn a phrase like a diamond lathe!
Or is that a quote, (which still impresses me)?
I’m a dummy. Is a "Topkill" taking off the top of the risor (which, I understand, is bent over right at the BOP, not way above it as I first thought from some of the poor graphics we started out with–as well as my own poor understanding of terms and such), and putting some kind of capping mechanism over the top?
I had thought a Topkill was loading down a vertical drill pipe with heavy mud and such until it overwhelmed the inherent pressure of the well. In this case, it doen’t seem like we have that vertical drill pipe to work with, unless we can inject the mud underneath the BOP.
Which I think seems reasonable, as is a junk shot under the BOP to close things up. The Topkill and junk shot are different things, I believe.
Did I get it right?
Thanks also to LisaDenise1 for the video of the leak. I came here to post it, and you already had it done.
My goodness–that looks like a lot of gas! Are we still sticking with the 3000-1 oil/gas ratio?
HORIZON
Don’t be so fast to discount what 220 is saying. I find it hard to believe you would prefer to leave the oil leaking before trying to use a hot tap. although I would work at the inlet side myself.
I do not believe there would be any danger of causing a crack or rupture of the BOP by doing a hot tap on the inlet side of the BOP. I have done hundreds of hot taps, there are no stresses put on any of the lines. especially when you are talking the size we have here. and there are taps that are accessible made into the BOP itself that could be used. to just let the oil flow continue leaking because someone is scared the line may crack is criminal. cracks in steel pipe just don’t work that way. it is not glass. it is not any type of hardened of over tempered steel. if a crack was present under high pressure it would be leaking. and still, if there were a crack you could drill the crack itself and it would not grow. you stop cracks in steel from growing by drilling them on the end.
They could easily have sealed the BOP already if they had allowed a crew to work on plugging the BOP from the inlet side.
Can anyone decipher this?
KenBobb: plug inside the wellhead via pumping into the choke and kill line receptacles on the side of the BOP’s. The wellhead; not the riser.
Continue pumping down annulus until reaching depth of drillpipe and continue circulating down annulus and up drillpipe with a fluid of an ideal weight and gel strength, to render the well static ( dead). QED.
Mechanic: It will take a team of mechanics with great saavy, to accomplish any of this and a leader to know this and confront challenges. A leader unifies and enlists, not distracts and blames. BP must promote leadership or disband.
IntellectuNeck,
Right at 21:30 the Riser flow goes to zero, but the SPP doesn’t – it basically rises. The SPP rises, drops, then goes off the chart over a 30 minute period.
Can anyone explain that?
Kick came in via drillstring explains it for me on first glance. If the annulus is closed via shutting the pipe rams and/or annular, the riser flow stops. If there is no float valve nor TIW valve in drillpipe and the pumps are of the SPP tells you now you have a problem. Might have noticed the problem before as the WOB flutters tell a trained eye there is trouble. Aka influx.
Also tells me the drillpipe size. See flowrate 1000 gpm? And the SPP 2500 psi. Big pipe. See hookload ~350,000 lbs? See bit depth 8367′? See 16 ppg mud? Calc. Bouyancy and I get 6-5/8" drillpipe. not sure what block weighs yet sure the drillpipe is the biggest. Perhaps the 16 ppg mud is incorrect and there had been some or all of this displaced to sea water since the hookload and bouyancy doesn’t completely jive.
Notice the WOB? Not supposed to happen. If the well kicks in annulus the string weight loses bouyancy and the hookload increases and the WOB goes negative.
Notice the pit volume and trip tank. 50 bbl gain not enough for 6-5/8" drillpipe yet the last bbls blasted into the air lifting the blocks and creating the first thud going up and second coming down.
First glance tells me the only way the hookload decreases during this kick is if the kick is flowing on the inside of the drillpipe. Perhaps the pipe rams and/or annular were shut. See 21:30? The riser flow stops? Were the pipe rams and/or annular shut then? See the SPP then at 1200 psi the up to 1800 psi averaging 1500 psi for the next ten minutes. 20 minutes before the well blew out? This might explain the kick coming up the drillpipe and the fact that with the bouyancy if 16 ppg mud the hookload would have been less actually. If all this instrumentation values are correct. This is first sign of trouble for an experienced hand. Of course the hookload gyrations at the end…did they have a TIW valve or similiar on drillstring and try to shut it at that point? Did the pumps pop off valve pop off? Any drillstring check valve? If all of my interpretations are correct then obviously no. There weren’t internal check valves in drillstring or else no one on the rig floor saw the warning signs or was alerted in time to close them.
If this reasoning is correct, the annulus might contain a restriction (pipe rams, annular, downhole packer or test plug), and this might be holding back flow from the riser. Didn’t someone mention the first riser leak, just past the kink, is relatively small? Perhaps the flow is still mainly from the drillstring with a small leak up the riser or at a the shear rams that partially cut drillstring. If so, the "top kill", wellhead plug or junkshot, would have to seal the pipe ram and/or annular leak To allow actual bullheading to reach another 8367′-5000’=3367′ and enter the drillpipe, yet if it was cement, and my interpretations from this new instrumentation data is correct this is possible. I see the situation differently now if my interpretation of this instrumentation data is correct and this indeed becomes a true top kill, bullheading kill possibility. Messy, yet not more so than already, and feasible. Perhaps. Pump a small bit of a junk shot first to plug pipe rams if these indeed are shut and partially sealing. 3367′ isn’t too far to bullhead. And once the bullheaded fluid travels the ~3367′ to 8367′ it would travel back up the drillstring to surface and choke off the influx of oil, if sufficiently viscous, and or heavy (cement being both).
Alot of interpretations not yet substantiated and interventions not clearly feasible.
If this was a negative test on a liner lap after only 16 hours of waiting on cement. Perhaps hasty, yet every cement job requires more or less time to reach full compressive strength depending on composition and temperatures and pressures of the annulus it will fill. Channels are avoided by having the hole filled with mud that is a condition to be displaced by the cement (flat gels), and circulated above the turbulent flow rate. Any of the factors might allow a channel in the annulus to form whereby the gas might have a path past a liner top and subsequently all the way to surface with oil flow following close behind. Liners are notorious for problems like this or else the liner top packer would never have been invented nor first used.
Some people, including myself, avoid liners like the plague for this very reason. Yet wince during negative test when forced, for whatever reason, to do so.
Still believe if shear ram technology were better, this could be avoided. A tool jt across a shear ram is a 1/16 chance. Liner tops and gas happen alot more than people know. The BOPE must handle the accidents.
Any more data?
energycommerce.house.gov/index.php?option=com_content&…
Things we now know from the daily drilling reports.
The mud weight in the hole was 14.0ppg
The casing was cemented and WOC time was 16.5 hours before pressure testing (This could be the kicker if the cement was not fully set, the added pressure in the casing would have expanded it, and created a micro-annulus in the cement or fracturing it allowing gas and oil to migrate up into the annulus).
They were working with a 3-1/2" tubing stinger, 817.70ft + 2 crossovers to get it to 6-5/8 DP.
The balance of the string was 6-5/8" 32# DP to the rig floor
They did run in and displace the hole and riser to seawater at 8,067ft (3,000ft below seabed)
They did run and pressure test the casing hanger seal both positive test to 10,000psi and a negative test to 1,400psi. Both were good.
We now have a stack layout drawing, showing ram arrangements.
The casing was 9-7/8" 62.8# which is 5/8" wall and 8-5/8" ID
The 7" properties are still unknown.
BIG HAT Tip to savagenatasha Thank You for the link to the house report.
Perhaps they spent those last few hours chasing a phantom pressure anomaly. Something was wrong, but whoever was looking at the data didn’t make the connection.
I read somewhere that a ROV picked up a wireless signal from a pressure sensor down in the well, and they also got something from the BOP, and those two readings gave them more confidence in the junk shot/top kill option. Perhaps well pressures are lower than expected, possibly even dropping, and the pressure after the obstruction/closure in the BOP is even less, suggesting that the well can handle the entire pressure of the formation once the leak is plugged.
Ok. 14 ppg makes more sense. The drilling recorder showed 16 ppg and the morning report 14. I hadn’t read the morning report yet.
Man can resist everything except temptation, and the temptation here at a cost of over $20,000 / hr would have been to skimp on the time to let the cement set and harden. Reducing the hydrostatic via displacing the 14 ppg mud with seawater early would have allowed a small conduit via a microannulus. This is the reason I like to bump plugs with seawater is so this microannulus isn’t allowed to form. Opponents of this are afraid the floats won’t hold. Proponents know HTHP double latch down equipment exists to add redundant equipment to hold.
Young engineers beware. Wait the full time for cement to set according to the pumpers guidelines for the slurry.
Also think twice before performing a negative test via a replacement of Wellbore fluid without float equipment in the drillstring. Big no, no, if this was the case. Displace a cement job with the lightest fluid that won’t test the upper limits of the pressure rating of the floats. Use latch down floats, anytime possible. Use Gas Check additives. Wait on cement to harden before conducting negative test.
Have redundant drillpipe safety valves during negative test. Drill floats on bottom, and TIW valves on rig floor. Had 20 minutes warning via hookload and SPP and much more via pit gain indicators of a kick. Time to replace heavy mud via well kill procedures if it had been recognized. Watch hookload readings. This is often the first and easiest indicator to recognize a kick. Set alarms on every known indicator. Hookload, WOB, pit gain, flow in, flow out. Always use real time monitoring back at headquarters. I have this on my iPhone at all times. A little nerdy yet it keeps rig personnel on their toes because they know you’re watching. The story of the "Three Little Pigs" comes to mind.
Defending the operations mistakes as pretty common and claiming this was a failure of the Deepwater industry to innovate failsafe BOPE is still true though..
InterestedEngineer,
The answer to your question is, that the pumps stopped because the power was cut, the pressure increase is not real, it’s caused by the wires burning through and shorting out. If you will notice the indicator line is starting to come back in towards the bottom this would trigger a change in scale if the system were still functioning.
PetroleumEngineer1,
The 16ppg reading comes from the mud pumps suction line to the mud pits, They were circulating seawater which comes from it’s own feed line from the deep well pumps on the rig, it doesn’t run through the densitometer. The chart reading shows what was pumped last before the pit suction valve was closed, which was a 16ppg slug which was pumped to draw air into the string for the negative pressure test on the casing hanger seals.
I have idea (new !!!!I do not) know it) for how to stop the spill in the Gulf. It consist in inject brine or/and salty water inside the pipe production. Locating a tubing in the oil production. You can computer the depth and longitud of the tubing and too computer the density of the brine inside the pipe production to get a good equilibrium with the brine column and well pressure to stop the flow. With a big pump near of the bottom or above a ship we could inject the water solution with big volumenes until the flow will be stopped.
Other fluids could be injected combined with sands, but I prefer the brine solutine because you can remove it easy to recover the well.
Horizon:
No. Not buying that. There is every indication that the readings are real. If all the power goes down, my thought is that is the time the transmission ends; not before. Alot of times methane shuts engines off due to robbing needed oxygen. This means power on during pressure spike. Gas to surface causes a pressure drop. This rise would have been recorded and was. The explosion comes later with a spark. As for the scale change, it doesn’t appear to in that mode though some systems do have that functionality. It overlaps as it goes off scale like some recorders do.
Horizon: Correct. The 16 ppg reading was the slug pumped the day before.
We observe from the government testimony that the BOP shear may even have had a ram missing, and that there was a hydraulic leak somewhere as well. I have read quite a few threads where engineers and oilmen have been talking about the BOP assuming that it was correctly configured and that its systems were healthy. Now it appears we won’t know what went on inside it until they get it up on deck and take it apart, which process should be REALLY interesting.
It also occurs to me that if the BOP annulus appears to have been sealed around the drill pipe, that perhaps it still is, and the leakage is coming from the drill pipe only. Since drill pipe can’t stand being bent, perhaps it is broken somewhere along the twisted and kinked riser, which would cause oil to come out of the riser.
I was just looking at the side view picture of the kink in the riser above the BOP. Does it look to you that there is a drill pipe in there? The bend looks awfully thin there from what I see. How long is the section of drill pipe pulled out of the riser pipe?
Maybe it sheared it off and shat it out. Maybe that’s why it’s sticking out of the riser so far.
If so is it in the BOP?
Have they tried to operated the hydraulics? even if there is something in there I think it would be a good idea to keep working them to see if they can get something closed.
Not sure where this fits in….either mitigation at the surface or help with the Hydrates. Any thoughts of a near leak point delivery of pure oxygen or LOX. Not sure if spontaneous combustion would ensue or if additional ignition would be required to get it going.
PetroleumEngineer1,
Not being argumentative, but the engines on a modern offshore rig, and most new land rigs are equipped with gas detection systems, if these systems detect flammable gas at the air intake filters they shut the engines down, by cutting off the fuel and dropping flappers over the air intakes, this happens in seconds, the system also kicks out the connections from the gen sets to the main buss in the SCR room and the main switchgear panels. The rig goes dark until the emergency gen set kicks in, and if gas is detected there or the ESD system has been activated it doesn’t start either.
The pressure increases and decreases are caused by pump activity, look at the flow in and flow out, the flow in is done by electronics counting triggers on the pumps input drive shaft with proximity switches, they will show flow rate even if the pump suctions are closed and no fluid is moving, however if you look at flow out it matches pretty closely with flow in. And if you look at the WOB line it shows where they were pumping in in a hurry, they were trying to kill the well. The WOB line doesn’t mean much as far as actual set down weight, unless they zero it when they tag bottom, it works just like the Martin Decker line load scale on the drillers console.
The main pit volume is increasing because they are displacing the 3,000ft of well plus the riser to seawater, this mud would would be sent to the pits until it became too diluted to be of any value, then dumped overboard after that, also remember there was a supply boat tied up taking off mud at the same time this was going on, so the pit levels were not static. The spikes are indicative of transferring mud from one pit to another to fill it up so the boat could keep unloading. The part that bothers me is from 20:02 to 22:22 there are 20minutes that the pumps were running and the pressure was going up, but there were no returns at the flow line, and the gas units are increasing. That could indicate they were pumping down the drill pipe but taking returns up the choke line, Or the riser was empty and there was gas contaminated air being pushed up the riser to the flow line.
I wish we had the records from the day before and during the cement job.
Horizon said: "220mph, I sincerely hope they don’t mess with that riser until the well is killed, or at least until they know the pressure inside it. Disturbing that riser would most likely cause the small leak there to become much larger, you have to remember it didn’t start leaking until the day after the rig sank, that indicates that the steel there is under tremendous stress, attempting to punch a hole in it may cause the crack to grow, or for the kinked area to fail completely.
The leak there may be a small crack under high pressure (Most Likely) or a fairly large crack under low pressure (Not Likely)."
I am not talking about trying to hot tap the riser at the BOP any long … but rather once it is on the seabed some distance away … they already know the pressure in that section as tyhe video from yesterday gives a very clear indication …
Since the end of the pipe is essentially open there is no restriction … and a HOT TAP upstream toward BOP would create no additional pressure …
Only AFTER the HOT TAP was in palce and a new temp riser pipe attached and opened would you cap the end … the current leak …
And capping that leak should have little or no affect on pressure in the line as the hot tap would then act as the [pressure outlet just as the leak does now
This would contain the majority of the oil and gas leaking and allow time for other kill measures etc to be completed
Another thought just occurred to me, maybe we should be pleased that the shear rams can’t cut the pipe.
If they do cut it that means 2,200ft of 6-5/8" DP an 822ft of 3-1/2" tubing are going to head south faster than a rocket leaving a launch pad, which by itself would not be a huge big deal on a normally cased and cemented well, it would just be some junk fishing when they reentered it.
But on this goofball design with the tapered string and no cement back to the crossover from 9-7/8" to 7" that this falling drill pipe will hit that crossover like a freight train on VW bug.
I would bet a couple of paychecks that it will knock the crossover right off the end of the 9-7/8" and curl up a couple of hundred feet of 7" with at least one 8-1/2" OD tool joint jammed in it.
This would genuinely open up the well to full flow through the 9-7/8" with an entire production zone open to produce. Not just squeaking through a casing hanger.
Horizon: you made my point exactly. The power would have gone off after the gas hit surface and this would have been after the last 20 minutes recorded. Remember the pressure would have been going up and if the flow was coming up the drillpipe there would be no positive flowrate shown. Now once this gas gets to surface the pressure would go down yet right after that as the generators shut down and the recorders stop recording. Also I agree the slashed are the mud being displaced by sea water and then transferred.
The WOB of course isn’t real since they weren’t drilling yet to an expert it is simply on a fine scale and indicative of a change of hookload only possible with a Downhole change in either flow or fluid or both. For Heavens sake there is no problem with arguing. We are after the truth not a prize for pointing out the most details. I just don’t have alot of time to blog and I’m doing this with one finger on an IPhone.
Keep in mind two things on that drilling recorder. When is the riser displaced? Later, during the last 20 min was the annular shut? I already said I think so.
Horizon,
No offense Horizon, earlier in this thread I made a comment.
HammerMechanic says:
I hope someone at BP has the sense to gather a team of their millwrights and fitters and let them brainstorm the problem of shutting the flow down. Too often the simple fix will be overlooked by stressed out, highly educated engineers when the guys that work with the equipment everyday can stand back and see the forest. The more heads the better. No insult intended to the engineers. Just saying, that a lot of good experience often gets overlooked.
Well you have been proving just what I was saying. You have torn down every idea thrown out is this thread and some have had some very good merit to them. Granted you seem to have a lot of good info, which is essential as to dealing with this type situation. And we all appreciate that. But I hope to hell the people that are doing the real decision making aren’t caught up in this same scenario. The oil is still leaking and the problem needs dealt with. What looks good on paper and what will actually get the job done in the real world situations are not always the same. You need to stand back and look at the conditions that actually exist and do what ever it takes to get the job done. Standing back and waiting for the safe/looks good on paper fix will not stop the oil. I have seen some very unorthodox ideas save the day over the years.
In my experience it takes both perspectives to get the job done when your feet are to the fire. Don’t be so fast to dismiss ideas that may not sound good when the news comes on, but may just stop the oil. There are a lot of knowledgeable people following this thread. Someone here may well come up with the solution. Or perhaps you just want the oil to continue leaking.
Sorry all. I will STFU now and go fishing. Nothing from this thread will even be looked at by anyone that matters anyway.
Hammer,
Discussion of ideas is how problems are solved, I have learned through many years of experience what works in theory, most often will not work when applied in real life. That is when perseverance comes in, if an idea doesn’t work try something else.
This particular incident poses new challenges that have never been presented before. This is the first subsea blowout that has ever been dealt with at this depth.
It’s like the freezing idea, it works in shallower water, but not at 5,000ft because for liquid nitrogen to be cold it has to boil off, that is how it takes heat from the liquid, at 5,000ft the pressure is too great for it to boil off at 42degF, it would just set there and be at seawater temperature. If you open the top of the vessel it will float out just like oil and would not boil until it reached the pressure and temperature it needs to do so, then it will begin to get cold. To get it or CO2 to boil at 5,000ft you have to heat it, that defeats the purpose of freezing the oil.
I know what happens when materials are pushed beyond their limits, I have seen many failures when its done, and have experience in what not to do with stuff that is already broken, it usually makes the situation worse if you mess with it until the conditions are favorable to do so, and you have had time to think about a method of approach.
I did some poking around, and the reason many of us with experience in the biz, have not seen this type of well design before, it’s because it’s a one off experiment, it’s the first time its been tried at these depths. Some genius with BP at the SPE in Alaska dreamed it up in 2007. Like many other things the design has merits, It would be OK in a known area say on a multi-well production platform where they drill the same formations at relatively same depths over and over. BUT NOT FOR A WILDCAT.
I may have mentioned this before, but when you try to reinvent a wheel .. you usually end up with square wheels.
What BP needs to do is start listening to some old drillers that have seen their fair share of goofy stuff in their careers.
It’s like the big box they tried earlier, it would have worked fine if they had had it ready to place over the leaks and ready to take returns to surface BEFORE they lowered it over the leak, if they had done so the hydrates would not have blocked the top of the funnel. They would have headed north before they had a chance to bridge off and stick together, I know of at least 4 other engineers besides myself that sent that info in to BP and Transocean.
And yes the response teams do look at these threads, they have posted comments on several of the other pictures and videos.
latest …
basically a cork and a straw …. sorry but sounds silly to me – just do it right … it would take less than a day to build a proper HOT TAP saddle – with a gate vale on the tee annd a collar on top of that to properly bolt on new riser – riser pipe that could be the 19 5/8 inch and could still have pipe inside if needed …
And the saddle could have a bolt flange on the end as well – which would allow pipe to be cutoff and a cap installed
BP to put smaller pipe inside gushing pipe in attempt to stop massive Gulf of Mexico oil leak
By JEFFREY COLLINS , Associated Press
Last update: May 13, 2010 – 11:22 AM
HAMMOND, La. – BP officials say they have decided to first try sucking oil away from the gushing Gulf well with a tube that will be inserted into the jagged pipe leaking on the seafloor.
Company spokesman Bill Salvin said BP hopes to start moving the 6-inch tube into the leaking 21-inch pipe — known as the riser — on Thursday night. The smaller tube will be surrounded by a stopper to keep oil from leaking into the sea.
The tube will then siphon the oil to a tanker at the surface.
Salvin says engineers have to first move the smaller tube past seawater that has gotten into the riser. The seawater could mix with methane
Horizon,
Please expand on what experimental techniques were being used on this well. The latest "Drilling Contractor" mag, by chance, highlights offshore technologies. I was instantly curious how some of the new technologies, such as riserless mud recovery systems or dual-gradient drilling, might have affected the DH disaster. I never considered that such technology MAY already be in place on the DH, which was an oversight considering BP’s confidence in this rig and crew (coming off its record-setting depth a few months back). I would appreciate your and the group’s thoughts on all of this.
Well, the "small tube in the big tube" idea seems self-evident now. Why didn’t anyone think of it earlier?
As far as worrying about water inside it, just put some kind of rubber grommet around the end that can be easily inflated to make a seal, put the silly thing in the end, let the oil and gas leak around it, and pump down methanol until it starts coming out the end of the smaller pipe. Then inflate the grommet, seal the end and start pumping out oil!
A little negative pressure at the end of the broken pipe might also reduce the leak coming from the crack at the top of the BOP.
Seems like a Duh! and "Let’s get it done" sort of thing.
Only issue I see is the possible stresses that could be induced by a downpipe a mile long. But big anchors on the bottom should deal with that pretty effectively.